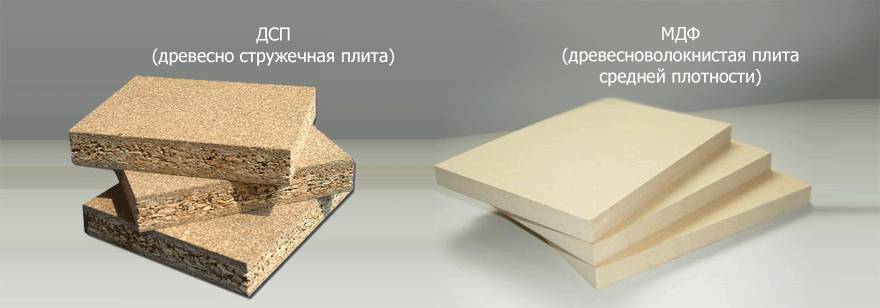
Photo: www.elvis-mebel.ru
“Sometimes a variety of goods is bad ...” - the visitors of the building and hardware store sigh, who have to choose between such similar panel materials as MDF, chipboard and laminated chipboard. At the same time, it is completely unclear to the non-professional that of the above can be used in this or that case. But to understand is not as difficult as it seems.
MDF (short for English Medium Density Fibreboard) is a type of fibreboard that has an average density and is produced by the method of dry pressing (at a certain high pressure and temperature) fine wood chips. It is clear that how much in this case, the raw materials do not heat or squeeze, chips will not hold each other. Therefore, they add a “binder” (something like glue) - melamine-modified carbamide resins.
The production technology of MDF was developed in the USA in the 60s of the XX century, in the same place in 1966 its industrial production was started. In Russia, the first MDF were released only in 1997.
Chipboard - chipboard (usually referred to as chipboard, although it is correct to use the abbreviation DSP) - is obtained as a result of hot pressing of chips (and other wood particles) mixed with a non-mineral binder. In this case, the MDP may consist both of a single layer, and of several layers (three or more).
Chipboard is produced in the United States for more than 70 years, in Russia - somewhat less.
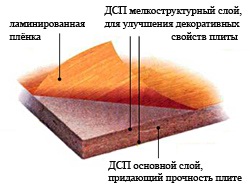
Laminated chipboard is a kind of chipboard that is a plate laminated with melamine films. The unity of the design is achieved by simultaneous exposure to high temperature and pressure. The surface of chipboard can be made both smooth and embossed (imitating the structure of wood or any other materials).
Security
The production technology of plate materials implies that the content of harmful substances in MDF is less than in the particle board. We are talking about volatile substances, harmful to humans, emitted by resins (used as binders), which gradually (during long-term operation) “evaporate” and accumulate in the air, if there is not enough room ventilation. All these substances do not cause instant lesions to the human body and have a harmful effect only after prolonged contact with them (in other words, if you decide to lie for a long time on a chipboard or MDF slab, you will die not from poisoning by substances released by them, but from thirst, hunger or from old age).
However, manufacturers still set a certain gradation:
- MDF - with strict observance of technology and the implementation of high-quality cladding of the construction surfaces from it is considered the least dangerous in terms of the emission of harmful substances into the surrounding air. In the production of MDF, the main binder is lignin released during wood heating. Therefore, high-quality MDF is environmentally safe;
- Particleboard class E1 - takes the second place in safety for the human body (but also only with appropriate surface cladding);
- Particleboard class E2 - allocates the greatest amount of harmful substances, is banned for production in foreign countries, and in Russia - is prohibited for the production of furniture and products used inside public and residential premises (GOST 10632-2007).
The difficulty of determining the harm actually inflicted by these materials lies in the fact that the information recorded in the certificates is not always true (and the certificates are sometimes not “native”, that is, compiled based on the results of the tests, but “purchased”).In addition, not all manufacturers (especially Russian) comply with the recommended process technology for the manufacture of MDF and particleboard, trying to save when using lower quality resins.
Cost of
The simpler the production and the more affordable the raw materials, the cheaper the material will be. Since the main raw material for the production of MDF and particleboard is waste from the woodworking industry, the following factors will affect the price difference:
- production technology (MDF is more expensive than particle board),
- manufacturing country (plate materials of foreign European firms will cost more than their Russian counterparts),
- the number of intermediaries between the manufacturer and the buyer (the more there are, the more expensive the material will be),
- the presence of additional properties attributed to the materials in the production process (fire resistance, biostability, water resistance),
- availability, quality and durability of the decorative coating on MDF or chipboard (everything that gives the construction of these materials greater safety and durability is more expensive).
What is better: MDF, chipboard or laminated chipboard?
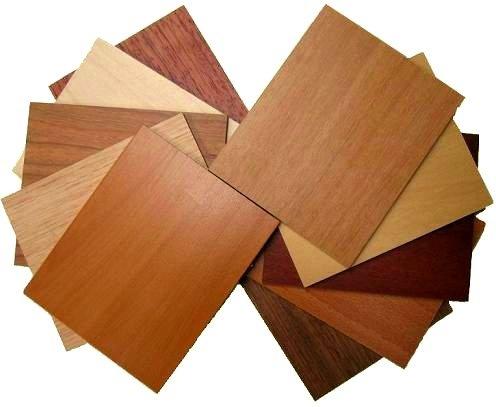
Photo: gklesprom.ru
Unfortunately, this question cannot be answered unambiguously, since MDF and DSP have their main purposes, in which their use is considered safe enough for humans.
So MDF and chipboard (LDSP) class E1 (with the obligatory facing of surfaces) can be used in the manufacture of furniture. In this case, special attention should be paid to the quality of the edges and seams between them and the layer (plate surface). If the seams are not performed with sufficient quality, then water will eventually get into them (for example, during wet cleaning of rooms) and MDF (like chipboard) will “swell up”. At the same time chipboard is much less moisture resistant.
But MDF is more responsive to high temperatures. Furniture made of MDF should not be placed too close to heating devices - it can warp.
MDF is a harder material, it does not crumble when milling - this allows making cutouts for fittings, creating drawings and carving on the surface. Unlike chipboard, MDF well holds screws and other fasteners.
But even if all the furniture elements are made with high quality, one should not forget that MDF and chipboard are mass-produced materials that are to some extent (according to different characteristics) inferior to furniture made from properly dried and treated wood. In other words, even the best furniture made of plate materials will not last more than 10-25 years (depending on the quality of the raw materials and the accuracy of handling it during operation).
It is also necessary to take into account that often in the production of furniture from MDF only facades are made, and walls and internal parts are made of chipboard. Furniture made entirely from MDF is quite expensive.
Another option for using MDF is the fabrication of door elements from it in the factory. However, when fitting parts on the installation site, it is worth paying attention to some nuances. So the trim plates made of MDF when they are trimmed in size turn out to be “unprotected” from moisture from one of the sides, which can lead to their deformation.
But the chipboard will be simply indispensable as a subfloor (as this material does not have direct contact with the air inside the room and, therefore, will not be able to release harmful substances into it). For the "safety net" can be coated with chipboard protective paintwork.