Today in the construction of porous ceramics can be (and is) considered an elite building material - deserved, by the way. The large format of the block with air voids has incorporated the main advantages of ceramic bricks with additional properties, such as high thermal insulation characteristics, for example. A wall of porous blocks can be laid out in a single layer, without subsequent additional insulation. In this case, the mechanical strength of the structure will not suffer!
Features of porous blocks
For the manufacture of material according to the process used construction clay, which is still in the raw form of wood chips. After adding the filler, the mixture of clay and chips is burned at a temperature of more than a thousand degrees. At the same time in the firing process wood chips just burn out, forming in the closed structure of the material a large number of pores, the volume of which reaches 50 percent of the total volume of future blocks. These closed pores and crevices prevent heat loss through the walls of buildings and increase the resistance to heat transfer. As a result, the wall with a total thickness of 45-50 centimeters fully meets the established requirements of heat engineering, which are imposed on external walls and walling.
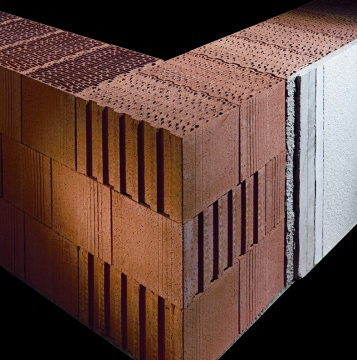
Due to the fact that the blocks have such a large number of internal voids, porous ceramic blocks are endowed with excellent additional properties: in addition to high thermal insulation, this is also high sound insulation, and excellent vapor permeability, and good frost resistance, as well as complete environmental friendliness and fire safety.
Mechanical characteristics: the average density of a porous ceramic block is approximately 2 times less than that of a conventional silicate brick (760-860 kilograms per square meter). Thermal conductivity is only from 0.15 to 0.29 W / m * degree (for a brick - 0.65 - 0.81), the strength of the blocks corresponds to the international mark M-75-150. Such strength is enough to build load-bearing walls for a seven-story building from ceramic blocks.
Types of porous ceramic blocks.
Basically, the types of porous ceramic blocks differ only in dimension. Moreover, their height is almost always a multiple of the brickwork. Therefore, in almost any case, the project of any house made of brick can be adapted to the masonry of porous blocks.
The standard width of such blocks is 25 cm. The length of the blocks can vary, usually it is 25, 30, 38, 44 and 50 centimeters. It is the length that determines what the wall thickness will be, because when laying, porous ceramic blocks are laid with the long side across the walls. The blocks are stacked both on an ordinary cement mortar and on glue, but experts advise using a special warm mortar for laying - its use increases the insulating properties of walls by 17 percent. A wall lined up in a single layer of blocks, even if conventional cement mortar is used, will always meet the type standards for the 1st climatic zone - this is the majority of Russian regions. If you use a warm solution when laying ceramic blocks with a length of 38 cm, you can ensure compliance with standards in almost any region of the Russian Federation. If you use conventional solutions, you will need to additionally carry out wall insulation.
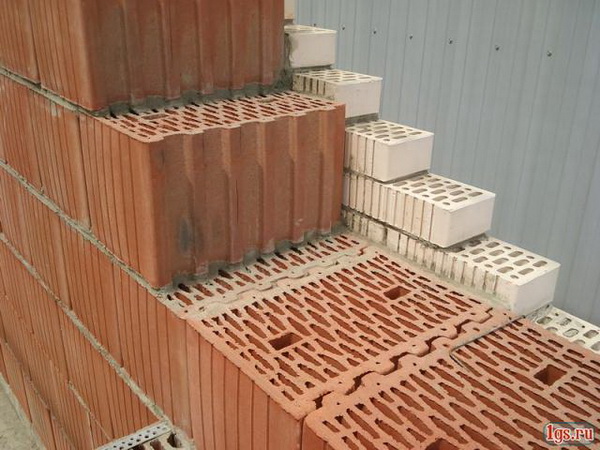
Photo: mekstroy.ru
For internal load-bearing walls of buildings and buildings, blocks of a length of 25 cm and more can be used; in addition, such blocks can be used for building partitions or for external walls with additional insulation. This applies if it is technologically impossible to increase the thickness of the load-bearing walls — for example, when the foundation is too narrow.Also, this method is used if necessary to maximize the ease of the whole structure.
Very small blocks with a thickness of 8, 10 and 11 cm are ideal for building partitions, as well as for facing any monolithic belts or as additional additional elements. Half blocks and corner blocks are used for laying right angles and laying angles of 135 degrees. Ceramic blocks designed for the device of internal walls have a slightly higher thermal conductivity than those intended for the device of external walls.
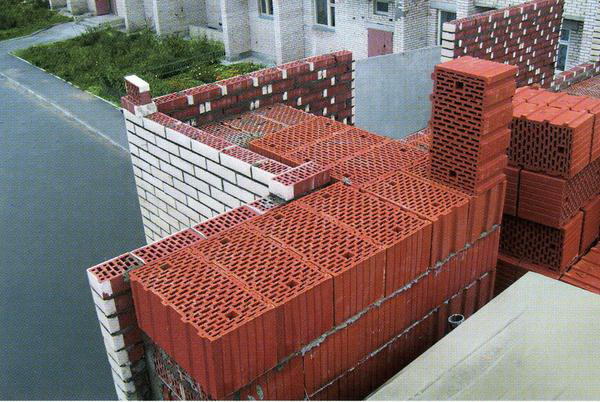
Photo: simferopol.olx.com.ua
Regardless of what construction and thickness the wall has, 16 ceramic blocks will be required for one square meter of wall construction, since in any masonry their width is constant and is 25 cm, the height of one row of masonry is also 25 cm.
Types of porous ceramic block walls
Elementary single wall - ceramic block and decorative facade finish. As a finishing material can be used facial ceramics or ordinary plaster. In the first case, a ventilated air gap and (mandatory) flexible metal connections between the main wall and the facing wall will be necessary for the final finishing of the wall.
Double wall It is arranged according to the “wet facade” principle: it is a ceramic block and rigid insulation material made of mineral wool 6–10 cm thick. in the main blocks, vapor permeability, otherwise excess moisture will accumulate inside the wall - for this reason you should not use polystyrene foam for insulation.
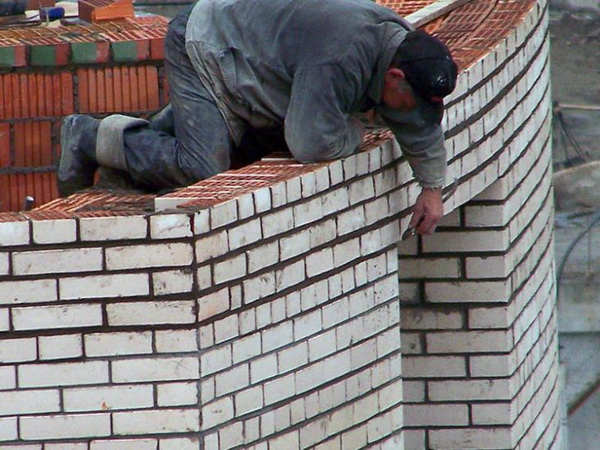
Photo: rostov.1gs.ru
Three-layer walls ceramic blocks are arranged with bulk or rigid insulation, which is located between the load-bearing walls of the blocks and exterior facing walls made of porous ceramic blocks with a length of 1 to 11 cm (this can also be a clinker brick or siding).
Features and high speed of laying blocks
Let's start with high speed. One porous ceramic block can replace from 5 to 15 bricks in masonry - of course, walls of such material will be built much faster than of bricks. In this case, a single-layer wall will have a specific mass of two times smaller than a brick wall, and it will be erected about 4 times faster. The largest porous block weighs no more than 20-22 kg, it is easily lifted by one person. The blocks are very close to each other, their special “groove-comb” system maintains a strong grip. As a result, laying one square meter of wall takes from a professional bricklayer no more than an hour.
The following features. It is desirable to build walls at a temperature of +5 degrees and above - this is necessary in order to eliminate the use of antifreeze additives (the use of additives significantly reduces the strength of masonry in compression). Moisten the blocks before laying - to do this, you can water each open pallet with a hose. The solution is not placed in vertical joints, except for the corners and joints of the external and internal walls. The seam in all cases should have the same thickness, approximately about 12 mm.
Some manufacturers of porous ceramic blocks advise to lay a close-meshed mesh between rows, so that the solution does not get into the pores. The cut elements are recommended to be used only in the middle of the walls, and to place them as far as possible from the corners and the places of interfaces.
The first rows of blocks must be laid on a leveled base. All corners of the structure should be located on the same level relative to the horizontal line - in the future any deviation will be extremely difficult to correct. Between the base and the actual first row of masonry, it is necessary to arrange a waterproofing layer.The laying should start from the corners of the building, no more than 3-4 rows should be laid vertically at the same time. Blocks should be laid close to the top, and not moved to the side of the bed.
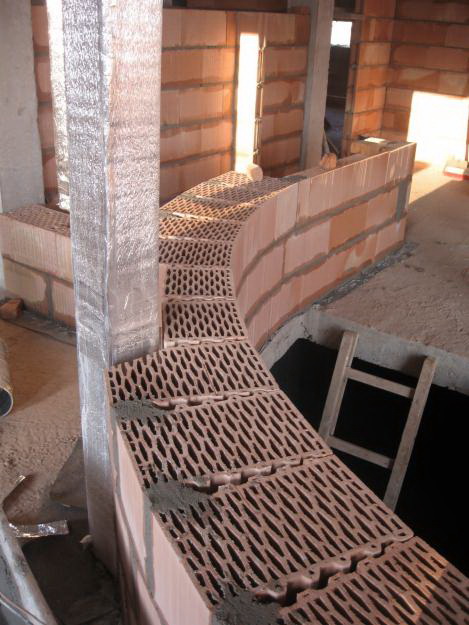
Photo: stroika-kazan.ru
Walls that adjoin each other, including internal and external, should be built at the same time, while interconnecting, “drowning” in each second row the blocks of the inner wall into the outer wall by about 10-15 cm. lining up later, in the outer wall for her need to leave the grooves. Internal walls can be made of another material, but not of ceramic blocks.
Major mistakes
So we got to the essence of the story. Since the material is fairly new in the modern building materials market, even experienced builders can make inaccuracies and obvious mistakes when working in porous ceramic blocks. Among them:
- Laying porous blocks along the wall grooved, long side. Such laying is not allowed even for the construction of internal walls, because it can break the adhesion of the blocks. In addition, the insulating properties of each unit separately in the perpendicular direction is much less, and the plaster for finishing work will take almost twice as much.
- Combining blocks with bricks and other building materials with a higher thermal conductivity is not allowed! This always leads to condensation of moisture on the walls, fungi and mildew, and so on.
- Lay rows of ceramic blocks without bandaging also unacceptable! This will significantly reduce masonry strength.
- Not allowed different thickness of seams between individual rows. This seriously violates the geometry of the walls, in the construction of which there are unevenly distributed loads. At the same time, the thick seams will be in operation by potential cold bridges, which will significantly reduce the heat-insulating properties of the walls.