Laminate, as a material used in construction, has long established itself from the best side, and this has gained deserved popularity. The main components of its success were its durability and wear resistance, at a relatively low cost. Plus, it is quite easy to install, which allows it to be installed quickly and efficiently. No less advantage, of course, is an attractive appearance and ease of care for him. But, along with this, this flooring would not have such excellent performance characteristics, if during its installation such an important component as the lining was not used.
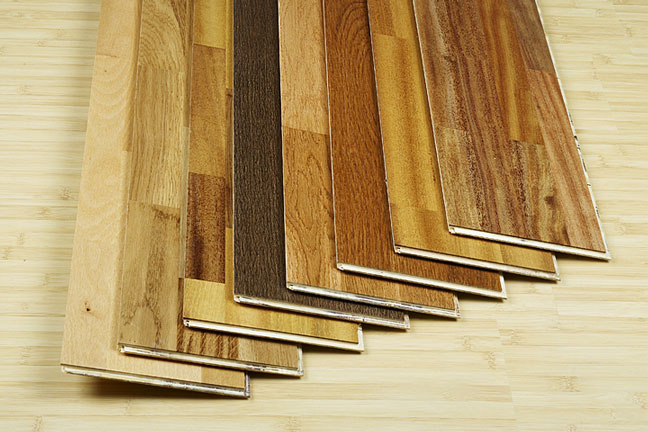
Photo: www.ualist.com
Let us examine all the advantages and disadvantages of the substrate under the laminate with our experts.
The functions performed by the substrate under the laminate varied. The main ones are undoubtedly: leveling, desiccation and sound insulation.
So function alignment - One of the main ones, since the base of the floor does not always have an ideal surface and is ready for laying laminate, because the substrate is a material that can smooth out minor irregularities and flaws in drops. But, at the same time, it is worth knowing that the ideal material in this case will be a substrate with a thickness of no more than 2-3 centimeters and a density of 20 kg / sq. M.
Moisture absorbing functionwhich is no less important, since the basis of multi-layer panel panels, which is laminate, is pressed wood dust, which has a paper coating on both sides. On the front side, such a wood-decorated panel has an upper laminated layer, and therefore a certain degree of protection, on the lower side, the base has a more vulnerable and porous coating, for which reason it needs
special waterproofing.
Soundproofing function. Due to the fact that the laminate itself is a fairly thin coating (in most cases 8 cm thick panels are used), this fact significantly reduces its sound-absorbing properties. In addition, this flooring is laid on the base of the floor using floating technology, which enhances the sound effect when walking, creating a resonance.
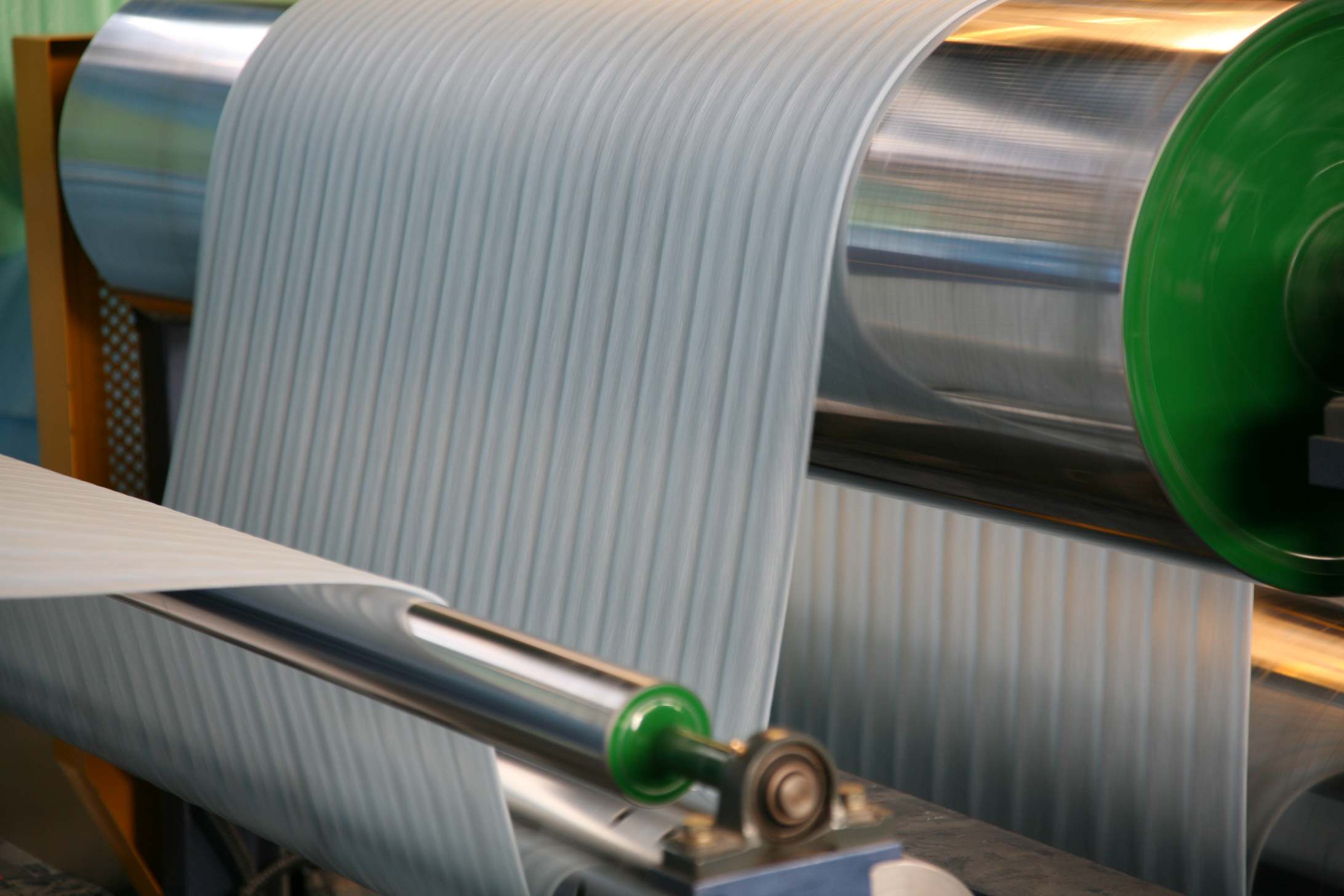
Photo: strmnt.ru
And now the question arises about what kind of substrate should be or what basic characteristics it should have. Let us examine this in more detail.
Durability - one of the most important criteria. And since the laminate has a rather long service life, the lining, respectively, should have excellent performance characteristics. The main parameters for determining the performance are the density of the material, which is measured in kg per 1 cubic meter. and directly affects the resistance to stress, which is calculated already in m. For example, a conventional foam polyethylene lining is the most democratic option, with a density of 20 kg / cubic meter. withstands an average of 700 to 900 kg / sq.m. The substrate is of higher quality and cost, according to the example of foamed polystyrene or cork, has a higher density - 30-45 kg / cubic meter, which accordingly increases its resistance to loads up to parameters from 3 to 6 thousand kg / sq.m.
Thermal insulation properties Substrates are an equally important factor that should be taken into account in the event that a floor heating system is present in the house. The increased thermal insulation properties of the material along with the thermal insulation properties of the flooring, whether it is parquet, linoleum or laminate, will reduce the efficiency of heating the room, which is unacceptable in this case.
Environmental friendliness - One of the factors in the choice, which many prefer the substrate, made using natural materials. But, it should be understood that the cost of such products will have a rather high cost.
Types of substrates
To date, the countless materials used as a substrate for laminate and parquet flooring with various technical operational characteristics are represented on the building materials market. The main ones are: tuplex, isoplat, foamed polyethylene foil substrate, extruded polystyrene substrates (arbitration, isoshum, heat), glass-fiber substrate and cork substrate, which also has several varieties.
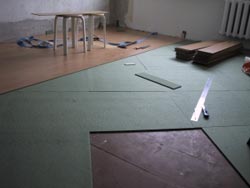
Laminate underlay isoplat (ISOPLAAT) is considered a versatile finishing and noise and heat insulating material. It is a sheet fibrous material made from natural pine wood species (100% ecological). It is possible to use it in a room with high humidity, as this material is able to absorb moisture up to 20% of its volume, while its insulating properties and geometrical parameters remain unchanged. Isoplatas and another series of wood-fiber materials (for example, Estonian "Silent move"), intended for laying under laminate, parquet and parquet, are called Silent floor.
Arbiton - Polish product made from extruded polystyrene using an additional layer of vapor barrier and adhesive tape. The use of this type of substrate eliminates the need to use a polyethylene film as a moisture insulating material when laying laminate. In addition, it provides excellent heat and sound insulation. This material has a uniform dense structure, which ensures a long service life, is easy to lay and belongs to the category of professional materials.
.jpg)
Photo: www.laminat-shop.ru Polyethylene foam
Izoshum - a substrate of extruded polystyrene foam from domestic manufacturers, which provides a decent level of insulation and sound insulation (reduces the impact level to 50%). This rigid sheet substrate is laid on the prepared substrate immediately before installation of the laminate or parquet flooring.
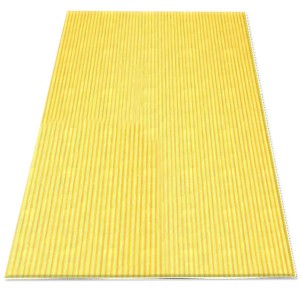
Teplon - polystyrene-based sheet material used as a substrate. Quite a tough coating that provides an excellent level of noise and heat insulation.
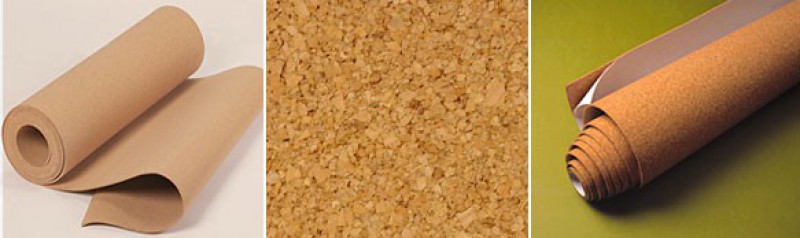
Photo: delaemremontvmeste.ru Cork substrates
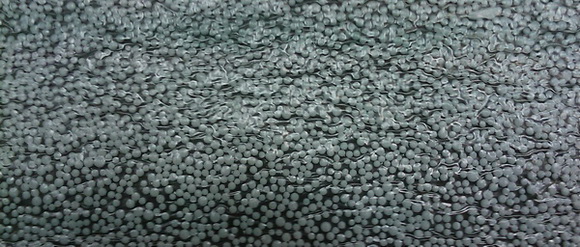
Photo: www.laminat-russia.ru Tuplex
The main disadvantages of different types of substrates
Foam polyethylene substrates are distinguished by one drawback - the inconstancy of the material thickness, plus the entire substrate of this type have an insufficient degree of sound insulation.
Expanded polystyrene - a substrate, the lack of which may be insufficient leveling ability. Therefore, the base for this material should be prepared with special care, avoiding significant differences in the level of the base of the floor (no more than 0.2 cm per 1 m.
The cork substrate, due to naturalness and high quality, has a fairly decent price, which sometimes becomes its main drawback. In addition, the substrate of cork chips has a low moisture resistance, because to use this material in rooms with high humidity, you should choose a rubberized cork substrate or cork coating with bituminous impregnation. In general, cork is an ideal material for use as a lining under the laminate. And only in the case of laying on a warm floor, its dignity (high thermal insulation) becomes a disadvantage.
For warm choose or special heating system for laying under the laminate (for example, ALLOC Heating System), or a very thin substrate that will protect from moisture and provide sound insulation, but will not interfere with heat transfer.
Styling Features
The basic principle that guides the choice of the substrate under the laminate, is the state of the base of the floor. The smoother and more perfect its surface, the smaller the thickness of the substrate should be chosen, while the stiffness class is also taken into account. The optimum is considered to be a thickness of 2 mm for the base with an ideal surface and 2-3 mm for the base having an uneven surface and defects. If you use the substrate of a thicker type during installation, it will rather damage the interlocking lamella joints and significantly shorten the life of the flooring, since the laminate will continually bend when walking.
The process of laying the substrate under the laminate does not present any particular difficulties, although it has its own particular rules. The process begins with the fact that the foundation of the floor is prepared, which consists in leveling the surface and its primer. Then you can proceed to the main action - laying the substrate. Different specialists recommend different ways of laying: some believe that laying the material along the lamellae of the coating is the most appropriate, others, on the contrary, across. The latter method is considered the most appropriate in order to avoid coincidence of the seams of the coating and the seams of the substrate, which is especially important in large premises. In this case, the deformation of the castle lamella joint is inevitable, which is accompanied by a characteristic creaking and crunching during walking (Moire effect).
Sheet lining stacks in staggered order without overlap and sealed with masking tape. The rolled substrate is laid with an overlap on the walls, but without an overlap on the subsequent strips with which it is also fastened with adhesive tape. Cork substrate is laid without overlap. For some substrates, a 0.2 cm thick polyethylene film is used as a vapor barrier, which is more often used for cork material.