7 best welding electrodes

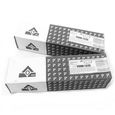
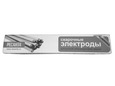
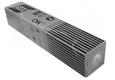
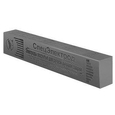
The review of the best electrodes for manual welding of carbon and corrosion-resistant steels was compiled using publications from the journals "Welding and Diagnostics", "Metallurgical Bulletin" and other specialized sources. The article summarizes the online reviews of professional welders on products from different manufacturers.
Selection criteria
Unfortunately, Russian electrodes lose to many foreign analogues in most parameters. However, "breakthroughs" in this area have already been outlined. The Russian electrode products, produced in a few joint ventures so far, are no longer inferior to many venerable brands in terms of quality stability. Some factories of national subordination began to "catch up" with them. However, in cases where it is necessary to confidently ensure high quality of the seam, professionals still prefer to use more expensive, but also better, electrodes of foreign manufacture. Electrodes of any type are suitable for welding inverters, not all types are suitable for AC welding machines.
When choosing the best electrodes for the review, we were guided by the following criteria:
- production volumes;
- product quality;
- getting the manufacturer in reviews on the electrode industry;
- feedback from professionals.
For the correct price comparison, we included in the review only the most frequently used electrodes with a diameter of 3 mm.
The main parameter of any welding electrode, which determines most of its properties - from the ease of ignition to the quality of the weld - is the composition of its coating. The most common today are the following types of coatings:
- Rutile Electrodes (and electrodes with a mixed coating on this basis - rutile-cellulose and so on) have become one of the most popular due to the ease of ignition, including repeated, reduced (within reasonable limits) sensitivity to damping. They can be used on both alternating and direct current in all directions of the seam, but when choosing a rutile electrode, you need to be careful - you can buy both a good electrode and a pollutant seam with a huge amount of slag ulcers, suitable only for tacks.
- Main coated electrodes Most often are used when welding by a direct current in especially responsible places. When burning, large amounts of carbon dioxide are emitted, which reliably protects the weld pool from exposure to oxygen. The seam itself is more plastic than when welding common types of rutile electrodes. The reverse side of the coin is an increased sensitivity to moisture and difficult ignition: cooking with such electrodes is much more difficult.
Category | A place | Name | Rating | Price |
---|---|---|---|---|
Best rutile electrodes | 1 | ESAB-SVEL OK 46.00 | 9.6 / 10 | 160 |
2 | Lincoln Electric Omnia 46 | 9.5 / 10 | 130 | |
3 | OZS-12 (SpecElectrod, Moscow) | 9.0 / 10 | 110 | |
4 | Resanta MR-3 | 8.7 / 10 | 160 | |
Top coated electrodes | 1 | Kobelco LB-52U | 9.5 / 10 | 350 |
2 | OZL-8 (LEZ) | 9.1 / 10 | 500 | |
3 | SSSI 13/55 | 8.9 / 10 | 100 |
Best rutile electrodes
ESAB-SVEL OK 46.00
160 (per kg)
Rutile cellulose electrodes, produced in Russia under the control of the Swedish concern ESAB. The electrodes of this brand can be confidently called one of the best in their price category - they easily burn even with partial dampness, can work in any direction of the seam on direct and alternating current, and the minimum current threshold required for steady burning is noticeably lower in comparison with other common types of rutile electrodes.Thanks to this, using OK 46.00 when welding thin-walled parts greatly simplifies the work even for a professional welder, not to mention beginners. These electrodes are not very sensitive to surface contamination and allow you to weld even heavily corroded metal without thorough pre-stripping. The slag formed in the weld pool is easily separated, the cooled seam has excellent strength characteristics and viscosity. Even a very damp electrode does not require any special measures for its “reanimation” - calcining can be carried out at a temperature of only 70-90 degrees. Main advantages:
Minuses:
|
![]() 9.6 / 10
Rating
Reviews
This is probably the best available electrode of this type. Particularly pleased that they are made in our country - the difference is huge compared to crafts of the FEZ or LEZ. |
Lincoln Electric Omnia 46
130 (per kg)
The American company Lincoln Electric has been specializing in welding for over a hundred years, and the first electrode with a coating that was created by it was launched on the market in 1927. The development experience was not in vain: the Omnia 46 electrodes with a rutile-cellulose coating recently released onto the market have earned the recognition of welders and a worthy place in the rating of the best welding electrodes from the Price Expert. Given the affordable price, they will be an excellent choice for beginners, as they easily flare up even on low-cost inverters without ignition relief functions. The length of the arc does not require precise control, since the electrodes are not very sensitive to its change within reasonable limits. When burning, the Omnia 46 produces a relatively small number of sparks flying around - and this is not only convenience in work, but also fire safety. Easy slag removal allows them to work on a rusty and dirty surface. The resulting seam is distinguished by high strength, comparable to many electrodes that have the main coating, which allows the use of Omnia 46 when welding pressure pipelines. Main advantages:
Minuses:
|
![]() 9.5 / 10
Rating
Reviews
Having bought a “sample”, I was very surprised by the quality of inexpensive, in general, electrodes: they light up like a Bengal fire, they burn evenly, without slagging the seam. |
OZS-12 (SpecElectrod, Moscow)
110 (per kg)
High-quality electrodes that are certified by NAKS for use in welding low-carbon steels at critical and hazardous sites. When using these electrodes, the seam is easily and evenly conducted, after cooling it becomes covered by an easily separated slag crust. Its strength is no worse than when using most types of common rutile electrodes, there is no tendency to cracking or the formation of large slag inclusions. However, all these qualities require compliance with two rules. First, the coating of the OZS-12 electrodes is one of the most sensitive to damping, which is not typical of rutile electrodes. Before each use, the electrodes require thorough roasting at a temperature of about 150 degrees for an hour, which makes them not the most convenient option for welding: in the end, the main electrodes will also have to be calcined, but they will provide a more durable joint. Secondly, the welding zone requires stripping - large inclusions of dirt from the bath are removed poorly, reducing the quality of the seam. Main advantages:
Minuses:
|
![]() 9.0 / 10
Rating
Reviews
It is best to buy them in small packs - so they have less time to dampen when stored.The dry ones give a decent seam even in the hands of the “garage Kulibins”. |
Resanta MR-3
160 (per kg)
Rutile electrodes such as MP-3 can be called one of the most common, but this is at the same time their main disadvantage: the products of various factories vary considerably in quality, and often it turns out to be very mediocre - hence the certain distrust experienced by welders for this brand. Electrodes manufactured under the Resant brand can be called successful (especially in comparison with LEZ electrodes of the same type). Having retained all the advantages of the series (ease of ignition and arc in any direction, the ability to work on rust), they do not have widespread defects as well - a tendency to the formation of slag ulcers and pores, recrystallization with an increased carbon content in the parts to be welded (although for high carbon steel still fit poorly). Their sensitivity to dampness is somewhat more pronounced than is usual for the MP-3, and the mode of calcination is also tougher: at least an hour at 150-170 degrees. Main advantages:
Minuses:
|
![]() 8.7 / 10
Rating
Reviews
Still, I can’t call the MP-3 the best of electrodes for someone other than beginners, but among other things, Resante managed to stand out and pleasantly surprise with quality. |
Top coated electrodes
Kobelco LB-52U
350 (per kg)
These electrodes are manufactured in Japan by a subsidiary of one of the largest metallurgical concerns of this country - Kobe Steel, Ltd. Their purpose is responsible welding of components from low carbon steels, where structurally there is no possibility of double-sided welding, for example, when welding pipelines. Hence, there are high demands on the ductility of the weld and the minimum amount of residual slags that cannot be removed from the volume of the weld pool. It can be said that the Japanese did it: the LB-52U electrodes are really capable of creating an even seam without shells and uneven penetration, they flare up perfectly and keep the arc. The strength of the seam is up to 588 N / mm2. Naturally, the applied base coating caused a number of specific features of the use of electrodes - prior to use, calcining is required at a temperature of up to 300 degrees to remove moisture, otherwise the burning of the electrode and the quality of the weld significantly deteriorate. There will also be a noticeable difference in the seams welded on direct and alternating current. Main advantages:
Minuses:
|
![]() 9.5 / 10
Rating
Reviews
Some of the best electrodes for use in a stationary post, but when working on the road, they are not so convenient, especially when repairing pipelines, they too quickly collect moisture. |
OZL-8 (LEZ)
500 (per kg)
Electrodes are designed for welding steels with a high content of chromium and nickel, primarily stainless. Use only on direct current reverse polarity, short arc. If these conditions are met, the welder can put a strong seam with a minimal tendency to corrosion and pokalka, which makes it possible to use OZL-8 electrodes when welding highly loaded nodes, including those working under alternating loads. After welding, a small amount of slag is formed, which is easily separated. The seam does not crack as it cools, but it should be quenched to eliminate the possibility of crystallization, which significantly reduces strength. Before use, it is necessary to heat the coating at a high temperature (up to 300 degrees). Main advantages:
Minuses:
|
![]() 9.1 / 10
Rating
Reviews
Although it is not the most expensive electrodes for stainless steel, it is quite possible to work with them - the seam is smooth and durable, not covered by corrosion. |
SSSI 13/55
100 (per kg)
One of the most frequently used carbon steel parts in welding is the basic coating electrodes. They are distinguished not only by the high strength of the seam, but also by its resistance to alternating loads - the constant cyclic effect of compression and tension does not lead to the rapid formation of fatigue cracks. The main merit of this is the coating material: its melt resembling resin effectively removes all slags from the welding zone, excluding the appearance of slag ulcers in the cooled seam - the main stress concentrators. After cooling, the slag acquires a characteristic form of solidified glass, it is easily cleaved from the seam. Alas, it is this plastering that is also a minus of the UONI electrodes: they are difficult to ignite (the beginning welder often succeeds only after long attempts), re-ignition even after a short break already requires stripping the end of the electrode: the plaster melt instantly “sets” at the tip, isolating the metal . However, having gained experience, the welder begins to understand all the advantages of electrodes of this type, obtaining durable and at the same time aesthetic seams. Main advantages:
Minuses:
|
![]() 8.9 / 10
Rating
Reviews
These are not electrodes for the amateur, but a tool for the professional who is able to cope with the “character” of the SSSI. But they are worth it. |
The correct choice of electrode requires many factors to be considered. For example, if you need to weld steel with a high carbon content, many welders will advise you to UONI electrodes - but not the fact that in inexperienced hands you get something good. At the same time, more convenient electrodes like OZS-12 will allow to get a better result - but only until you master welding the more difficult types of electrodes.
Storage conditions must also be taken into account: keeping most types of electrodes with a basic coating in the garage means condemning yourself to permanent and prolonged burning of the coating before welding, which itself can take literally several minutes, and rutile electrodes in this case will be more preferable, especially types with the lowest calcination temperature (ESAB OK 46.00, Omnia 46).